車刀是金屬切削加工中應(yīng)用最廣泛的刀具。車刀用于臥式車床、立式車床、轉(zhuǎn)塔車床、自動(dòng)車床及數(shù)控加工中心上,加工工件的回轉(zhuǎn)表面。
(本篇選自《數(shù)控刀具選用指南》第三章第一節(jié) 車刀概述)
一、車刀的分類
(一)按照加工工件表面類型
按照加工工件表面的類型,車刀可分為外圓車刀、內(nèi)孔車刀及端面車刀。
1. 外圓車刀 外圓車刀用于外圓車削,對(duì)零件的外圓表面進(jìn)行加工,獲得所需尺寸、形位公差精度及表面質(zhì)量,如圖3-1所示。
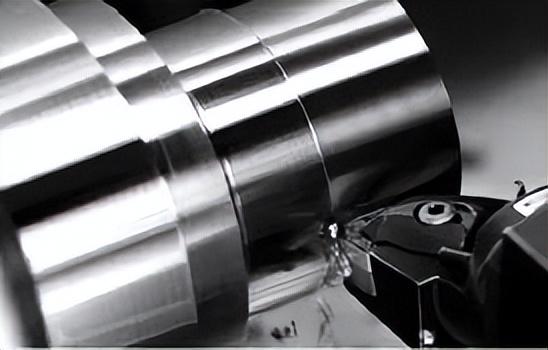
圖3-1 外圓車削
2. 內(nèi)孔車刀 內(nèi)孔車刀用于內(nèi)孔車削,如圖3-2所示,是用車削的方法擴(kuò)大工件內(nèi)孔或加工空心工件的內(nèi)表面;可以用大多數(shù)外圓車削的工藝方法來(lái)車削加工內(nèi)孔,此時(shí),刀具是固定的(與在加工中心中鏜削刀具旋轉(zhuǎn)方向相反)。進(jìn)行外圓車削時(shí),工件長(zhǎng)度及所選的刀桿尺寸,一般不會(huì)對(duì)刀具懸伸產(chǎn)生影響,因而能夠承受在加工期間產(chǎn)生的切削力。進(jìn)行鏜削和內(nèi)孔車削時(shí),由于孔深決定了懸伸,因此,零件的孔徑和長(zhǎng)度對(duì)刀具的選擇有一定的限制。
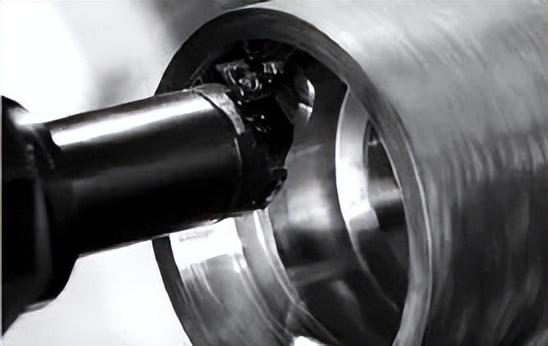
圖3-2 內(nèi)孔車削
3. 端面車刀 端面車刀用于端面車削,如圖3-3所示,刀尖始終處于與主軸軸線某點(diǎn)相交的直線上,結(jié)果得到一個(gè)過(guò)該點(diǎn)并與主軸軸線垂直的平面或錐面;端面車削刀具是指主切削刃能夠?qū)ぜ亩嗣孢M(jìn)行切削的刀具。
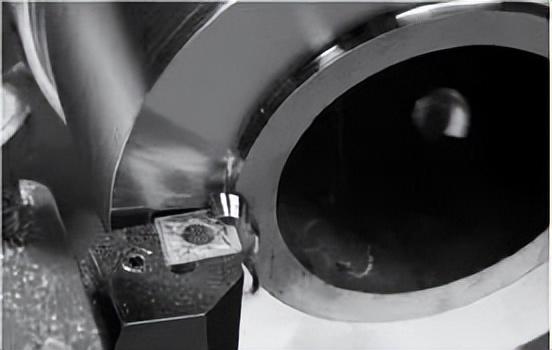
圖3-3 端面車削
(二)按照刀具結(jié)構(gòu)
按照刀具結(jié)構(gòu),車刀可分為整體車刀、焊接車刀、機(jī)夾車刀、可轉(zhuǎn)位車刀及成形車刀。
1. 整體車刀 整體車刀如圖3-4所示,是相對(duì)于焊接刀具來(lái)說(shuō)工作部分和柄部都是同類材料,或相對(duì)于可轉(zhuǎn)位刀具來(lái)說(shuō)指不可拆卸的整體式結(jié)構(gòu),通常整體車刀常選用的材料為普通高速鋼或高性能高速鋼。刀具剛性好,操作工人可根據(jù)加工需要,切削部分可刃磨成直面、斜面及各種成型面。
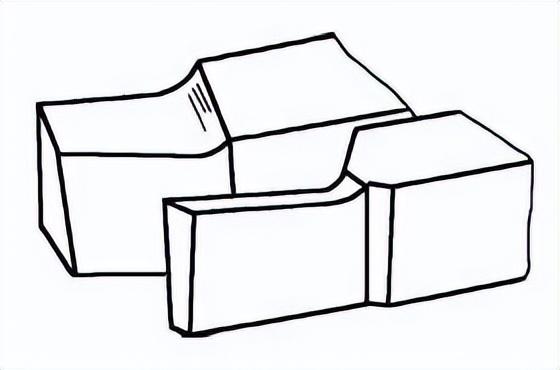
圖3-4 整體車刀
2. 焊接車刀 焊接車刀如圖3-5所示,是在鋼制刀桿上按車刀幾何角度的要求加工出刀槽,用焊料將高速鋼或硬質(zhì)合金刀片焊接在刀槽內(nèi),并按所選擇的幾何參數(shù)刃磨后使用的車刀。由于CNC車床和復(fù)合加工機(jī)床的普及應(yīng)用,加上焊接車刀在焊接后易出現(xiàn)微觀裂紋、硬質(zhì)合金性能降低等缺點(diǎn),已很少使用,但其整體剛性較機(jī)夾車刀和可轉(zhuǎn)位車刀為好。刀具磨損后可以進(jìn)行多次修磨,利用率高。
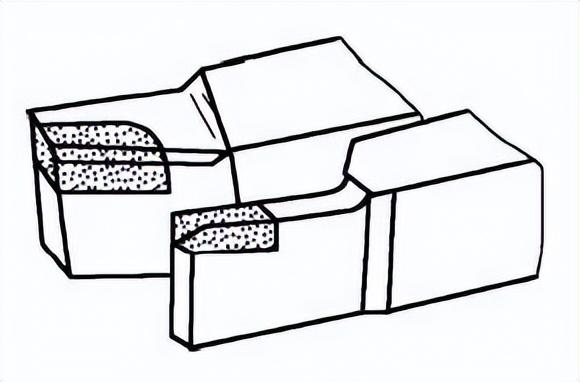
圖3-5 焊接車刀
3. 機(jī)夾車刀 機(jī)夾車刀如圖3-6所示,是用標(biāo)準(zhǔn)硬質(zhì)合金焊接刀片,用機(jī)械夾固的方法將其夾持在刀桿上使用的車刀,有如下特點(diǎn):
(1)刀片不經(jīng)高溫焊接,避免了因焊接而引起的刀片硬度下降、產(chǎn)生裂紋等缺陷,提高了刀具使用壽命。
(2)由于刀具使用壽命提高,使用時(shí)間較長(zhǎng),換刀時(shí)間縮短,提高了生產(chǎn)效率。
(3)刀桿可重復(fù)使用,既節(jié)省了鋼材又提高了刀片的利用率,刀片由制造廠家回收再制,提高了經(jīng)濟(jì)效益,降低了刀具成本。
(4)刀片重磨后,尺寸會(huì)逐漸變小,為了恢復(fù)刀片的工作位置,往往在車刀結(jié)構(gòu)上設(shè)有刀片的調(diào)整機(jī)構(gòu),以增加刀片的重磨次數(shù)。
(5)壓緊刀片所用的壓板端部,可以起斷屑器作用。
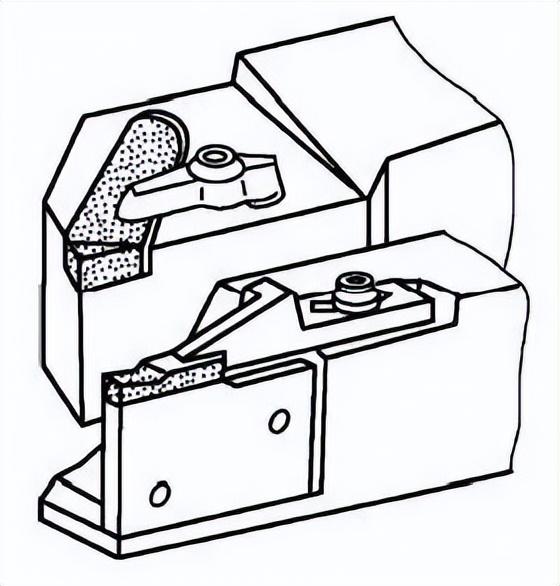
圖3-6 機(jī)夾車刀
4. 可轉(zhuǎn)位車刀 可轉(zhuǎn)位車刀如圖3-7所示,是使用可轉(zhuǎn)位刀片的機(jī)夾車刀。一條切削刃用鈍后可迅速轉(zhuǎn)位換成相鄰的新切削刃,即可繼續(xù)工作,直到刀片上所有切削刃均已用鈍,刀片才報(bào)廢回收。更換新刀片后,車刀又可繼續(xù)工作。

圖3-7 可轉(zhuǎn)位車刀
(1)可轉(zhuǎn)位車刀的優(yōu)點(diǎn)主要有以下幾項(xiàng):
1)刀具使用壽命長(zhǎng):由于刀片避免了由焊接和刃磨高溫引起的缺陷,刀具幾何角度完全由刀片和刀桿槽保證,切削性能穩(wěn)定,從而提高了刀具壽命。
2)生產(chǎn)效率高:由于機(jī)床操作工人不再磨刀,可大大減少停機(jī)換刀等輔助時(shí)間。
3)有利于推廣新技術(shù)、新工藝:采用可轉(zhuǎn)位刀具有利于推廣使用涂層、陶瓷等新型刀具材料。
4)有利于降低刀具成本:由于刀桿使用壽命長(zhǎng),大大減少了刀桿的消耗和庫(kù)存量,簡(jiǎn)化了刀具管理工作,降低了刀具成本。
5)能獲得穩(wěn)定的斷屑:斷屑槽在刀片制造時(shí)壓制成形,槽形尺寸穩(wěn)定,選用合適的斷屑槽形后,斷屑穩(wěn)定、可靠。
可轉(zhuǎn)位車刀由于有上述諸多優(yōu)點(diǎn),因此國(guó)內(nèi)外已經(jīng)公認(rèn)之為首選的車刀結(jié)構(gòu),也是應(yīng)用的發(fā)展方向。
(2)可轉(zhuǎn)位車刀刀片夾緊要求主要包括:
1)要求刀桿刀槽定位精度高:刀片轉(zhuǎn)位或更換新刀片后,刀尖位置的變化應(yīng)在工件精度允許的范圍內(nèi)。
2)刀片夾緊可靠:應(yīng)保證刀片、刀墊、刀桿接觸面緊密貼合,經(jīng)得起沖擊和振動(dòng),夾緊力也不宜過(guò)大,應(yīng)力分布應(yīng)均勻,以免壓碎刀片。
3)排屑流暢:保證切屑排出流暢,并容易觀察。
4)使用方便:轉(zhuǎn)換切削刃和更換新刀片方便、迅速。小尺寸刀具結(jié)構(gòu)要緊湊。在滿足以上要求時(shí),盡可能使結(jié)構(gòu)簡(jiǎn)單,制造和使用方便。
5. 成形車刀 成形車刀是加工回轉(zhuǎn)體成形表面的專用刀具,其刃形是根據(jù)工件輪廓形狀設(shè)計(jì)的,可用在各類車床上加工內(nèi)外回轉(zhuǎn)體的成形表面。用成形車刀加工零件時(shí)可一次形成零件表面,操作簡(jiǎn)便、生產(chǎn)效率高,加工后能達(dá)到公差等級(jí)IT8~I(xiàn)T10、表面粗糙度值達(dá)Ra6.3~Ra3.2μm,并能保證較高的互換性。但成形車刀制造較復(fù)雜、成本較高,切削刃工作長(zhǎng)度較寬,故易引起振動(dòng)。成形車刀主要用在加工批量較大的中小尺寸帶成形表面的零件。
二、車刀的選用
(一)刀具的合理選擇
在實(shí)際的切削加工中,車刀的選擇合理與否直接影響到刀具使用壽命和加工效率,也將影響到加工成本。車刀的選擇首先應(yīng)根據(jù)被加工工件材料來(lái)選擇最佳的刀具材料,然后根據(jù)實(shí)際切削中不同的加工形態(tài)選擇刀片形狀、刀具幾何角度、刀片斷屑槽形等,再采用合理的切削用量,達(dá)到最佳使用車刀的目的。
(二)車刀幾何參數(shù)的選擇
依工件材料不同,常用硬質(zhì)合金車刀的合理幾何參數(shù)選用推薦值見(jiàn)表3-1~表3-4。
表3-1 硬質(zhì)合金車刀合理前角推薦值
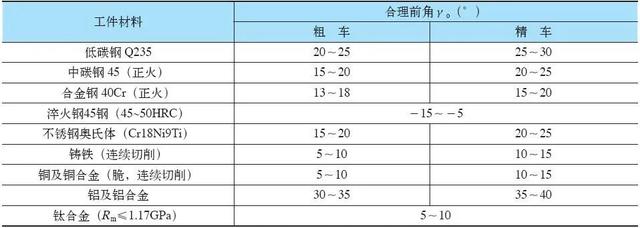
表3-2 硬質(zhì)合金車刀合理后角推薦值
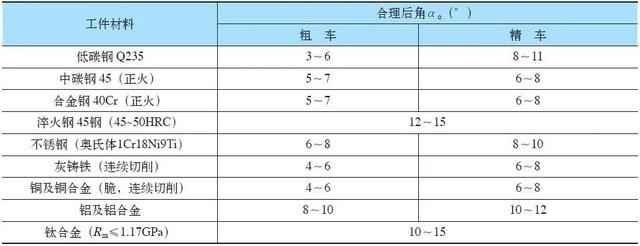
表3-3 車刀主偏角的選用

表3-4 車刀副偏角和刃傾角的選用
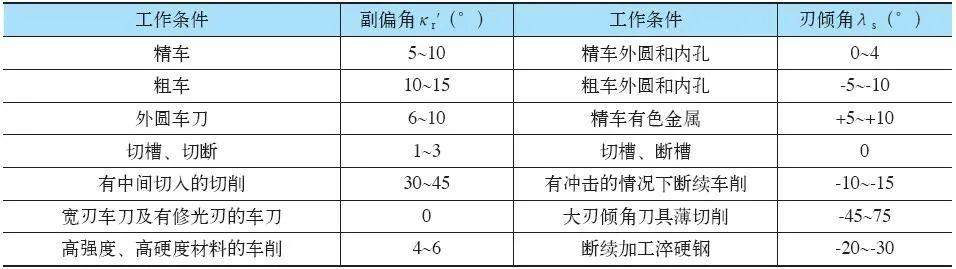
(三)車削合理切削用量的選擇
車刀合理切削用量的選擇見(jiàn)表3-5。
表3-5 硬質(zhì)合金刀具切削用量推薦表

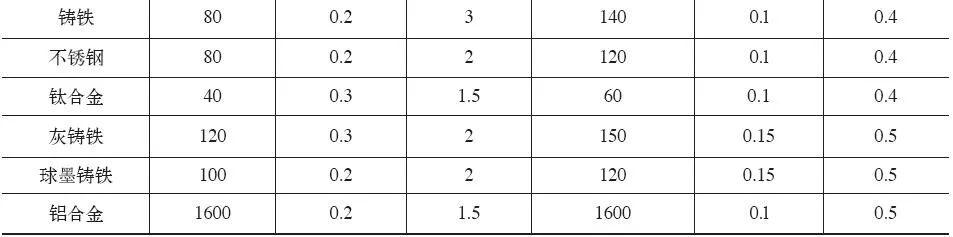
(四)外圓端面車刀刀桿和刀片的選擇
1. 外圓車刀刀桿的選擇 選擇車刀刀桿需要考慮到加工形態(tài)、刀具強(qiáng)度和經(jīng)濟(jì)性等因素。
(1)刀桿選擇主要根據(jù)加工形態(tài)。車削部位(外圓、端面、仿形等)與車刀的移動(dòng)方向(前進(jìn)式或后退式進(jìn)給)不同,能夠使用的刀桿種類也各不相同。
(2)各刀桿可以對(duì)應(yīng)的加工形態(tài)由安裝刀片時(shí)的主偏角決定。一般不要求90°垂直切削(直角加工)時(shí),如果選擇主偏角90°以下的車刀桿,可以選用正方形刀片的刀桿,比較經(jīng)濟(jì)。端面采用后退進(jìn)給方式切削時(shí),由于切屑處理的要求,需選擇主偏角105°以上的車刀桿與刀片。主偏角在95°以下時(shí)切屑處理非常困難,不推薦使用。主偏角在90°以下時(shí)不可以進(jìn)行后退加工。在倒角加工中選擇主偏角45°~60°的刀桿。負(fù)的副偏角為端面切削專用。
2. 外圓端面車刀刀片的選擇 車刀刀片的選擇與刀具材料的選擇同樣重要,需要考慮到加工工序、工件材質(zhì)、切削條件等。選擇最佳刀片可以提高加工效率、降低加工成本。
(1)刀片形狀的選擇,需要綜合考慮加工形態(tài)、切削刃強(qiáng)度、夾緊強(qiáng)度、經(jīng)濟(jì)性等。CNC車床越來(lái)越普及,可以同時(shí)加工外圓和端面的刀片應(yīng)用最多。適合這些加工的80°菱形刀片可以對(duì)應(yīng)粗加工到精加工的廣泛領(lǐng)域。仿形加工則使用55°菱形或35°菱形刀片。切削刃強(qiáng)度雖不如80°菱形,但卻能對(duì)應(yīng)最廣泛加工形態(tài)的形狀。選擇55°還是35°,需要根據(jù)工件形狀而定。其他的還有適合螺紋加工、切槽加工、切斷加工等的刀片形狀。
(2)刀片刀尖角越大切削刃強(qiáng)度越高,有利于斷續(xù)切削,但易受加工形態(tài)的制約。連續(xù)切削等穩(wěn)定的切削加工中,使用切削刃強(qiáng)度稍差一些、但刃數(shù)較多的正三角形刀片比較有效。選用刀尖角為82°的不等邊不等角六邊形的三角形刀片,可彌補(bǔ)此缺陷。背吃刀量小時(shí),使用保證切削刃強(qiáng)度的、等邊不等角六邊形(80°)刀片也很有效。圓形刀片強(qiáng)度最佳,最適于要求良好的加工面時(shí)使用,由于背分力大,加工細(xì)長(zhǎng)、薄壁工件時(shí)易發(fā)生振動(dòng),更換刃角時(shí)的管理也較困難。刀片尺寸大、厚,或立裝式刀片,其夾緊強(qiáng)度大,適合重切削。80°菱形刀片的切削刃長(zhǎng),可以兩面定位,所以?shī)A緊強(qiáng)度大,利于斷續(xù)切削和重切削。
(3)使用負(fù)角刀片時(shí),正方形刀片最為經(jīng)濟(jì),因?yàn)檎叫蔚镀瑔蚊?個(gè)刃、兩面8個(gè)刃都可以使用,而且刀尖角為90°,強(qiáng)度高。次之的是單面3個(gè)刃、兩面6個(gè)刃的正三角形刀片。
(4)刀尖圓弧半徑指刀片刀尖的圓弧大小。刀尖圓弧半徑越大,加工面精度越高、刀尖強(qiáng)度也越大,但會(huì)造成徑向分力增大,易引起振動(dòng)、切屑處理較難。另外,切削刃位置后退,加工直徑變大。相反,刀尖圓弧半徑減小,加工直徑隨之減小。一般使用的刀尖圓弧半徑范圍是0.4~1.2mm,但從刀尖強(qiáng)度角度考慮,重切削時(shí)要選擇大的刀尖圓弧半徑,精加工時(shí)則選擇較小的刀尖圓弧半徑。
(五)內(nèi)孔加工時(shí)刀片形式的選擇
內(nèi)孔加工時(shí)刀片形狀的選擇基本上與外圓加工時(shí)方法相同。但內(nèi)孔加工時(shí)刀具的懸伸量較大,無(wú)法進(jìn)行重切削,因此幾乎不需考慮不同形狀的夾緊強(qiáng)度問(wèn)題。
(1)隨著刀尖圓弧半徑增大,背向分力增大。背向分力使刀桿發(fā)生彎曲變形,必須防止發(fā)生振動(dòng)。背吃刀量小時(shí)需要注意刀尖圓弧半徑增大引起的切屑處理性惡化及切屑排除方向發(fā)生變化的問(wèn)題。內(nèi)孔加工時(shí)須從工件的內(nèi)部排出切屑,排屑方向發(fā)生微小的變化就有可能造成切屑排出困難。
(2)進(jìn)行小徑的內(nèi)孔加工時(shí),為了防止刀片與內(nèi)壁面干涉,若使用負(fù)角刀片,則需選用大的負(fù)前角。這樣做會(huì)使切削力增大,易引起高頻振動(dòng),所以內(nèi)孔加工中通常使用刀片帶后角的正角刀片。若加工直徑較大,從經(jīng)濟(jì)性角度考慮使用負(fù)角刀片較為妥當(dāng)。
好了,這篇文章的內(nèi)容發(fā)貨聯(lián)盟就和大家分享到這里,如果大家網(wǎng)絡(luò)推廣引流創(chuàng)業(yè)感興趣,可以添加微信:80709525 備注:發(fā)貨聯(lián)盟引流學(xué)習(xí); 我拉你進(jìn)直播課程學(xué)習(xí)群,每周135晚上都是有實(shí)戰(zhàn)干貨的推廣引流技術(shù)課程免費(fèi)分享!